기타는 주변에서 쉽게 접할 수 있는 가장 대중적 악기 중 하나다. 전 세계 공장에서 대량 생산한 기타가 시장에 공급되는 가운데 공정 하나하나에 정성을 기울여 자신만의 개성 있는 소리를 만들어 내는 수제기타 제작자가 있다. 1993년부터 클래식 기타를 만들어 온 이주용(61) 장인. 그를 경기 파주시 작업실에서 만났다.
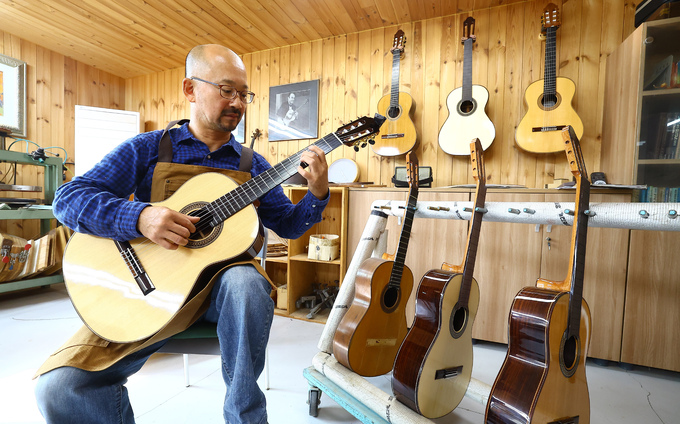
한적한 농촌 마을 끝자락에 자리 잡은 공방 내부는 기타의 주재료인 나무 냄새로 가득했다.
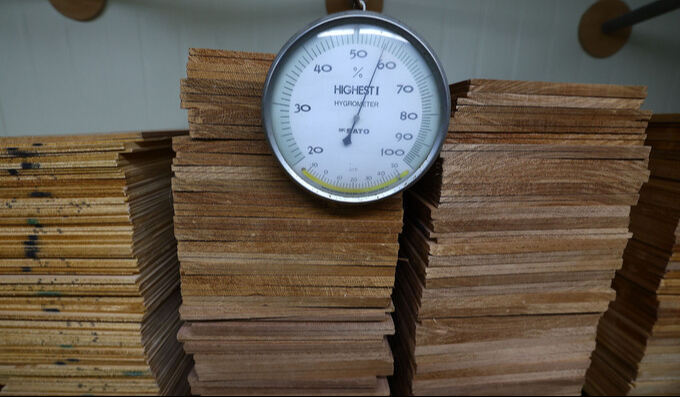
“목공소 분위기가 많이 나죠? 기타는 소리의 울림이 중요한 악기라 나무를 일정한 두께와 각도로 깎고 다듬는 공정이 대부분입니다.” 장인의 안내로 목재를 보관하고 건조하는 방을 둘러봤다. 습도계와 온도계가 달린 방 안에서 기타의 각 부분에 사용되는 다양한 종류의 목재가 건조되고 있었다.
기타의 몸통을 구성하는 앞판과 옆판 그리고 뒤판에 쓰이는 나무가 모두 다르다고 한다.
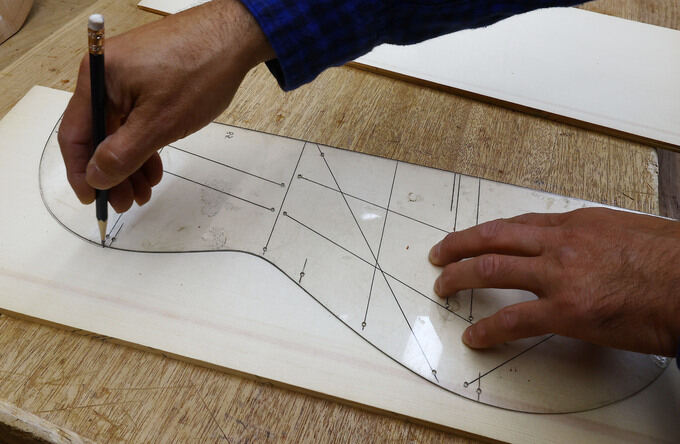
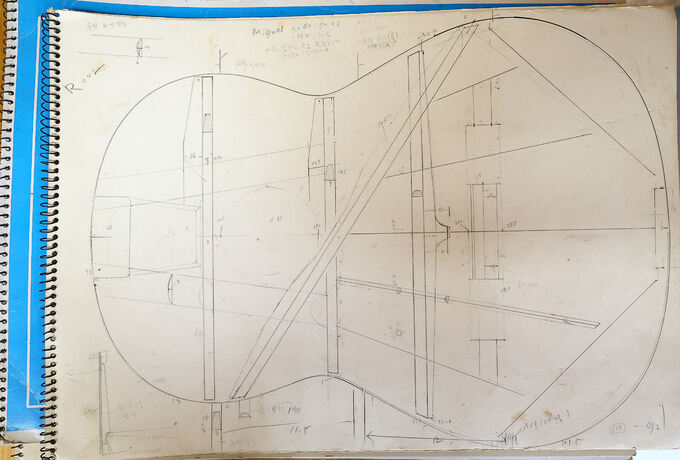
“나무마다 강도와 울림의 차이가 있어 기타 전체의 균형을 맞추기 위해 앞판에는 기타의 음색에 어울리는 가문비나무나 적삼목(스프러스나 시더)을 사용하고 옆, 뒤판은 인디언 로즈우드나 브라질리언 로즈우드(하카란다)를 씁니다.”
장인이 건조 중인 목재를 들고 손가락으로 톡톡 두드려 본다. 같은 종류의 나무를 같은 기간 동안 말리고 같은 두께로 가공했어도 모두 미묘하게 다른 소리를 낸다. 그 미세한 소리의 차이를 감지해 특성에 맞게 기타 제작에 사용하는 게 제작자의 실력과 연륜이다.
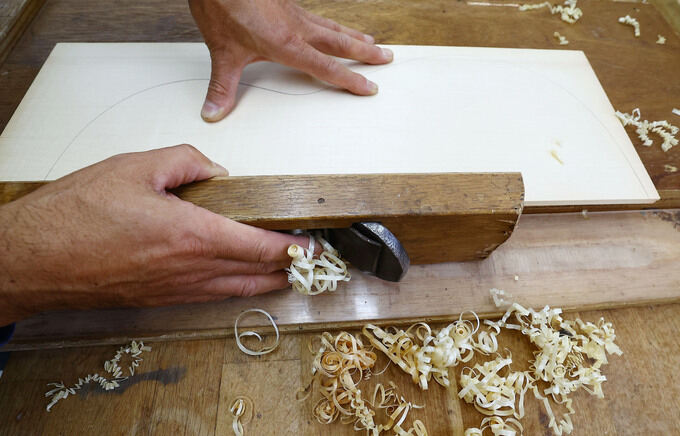
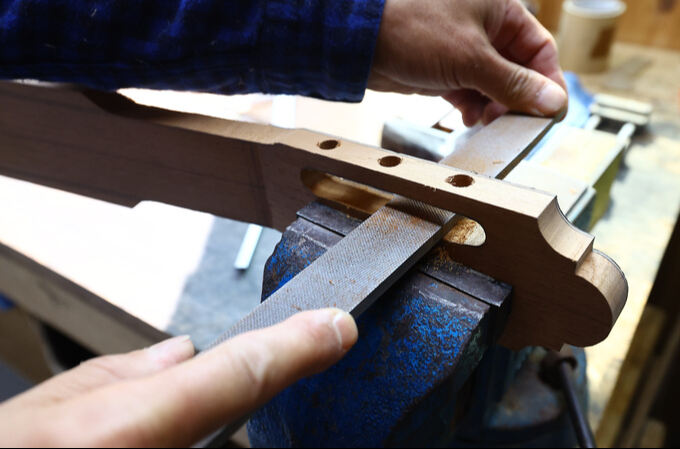
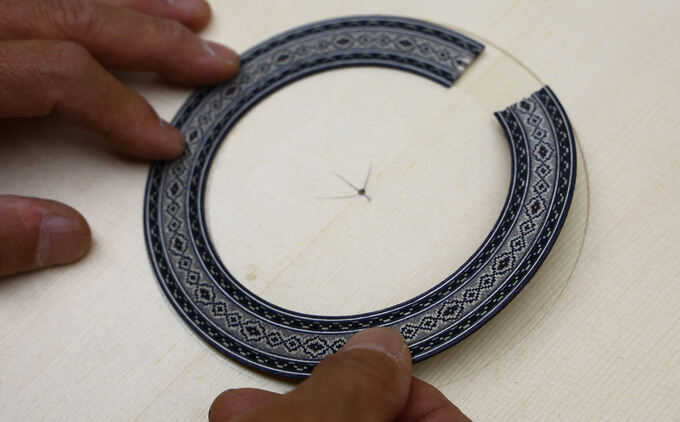
기타 제작에 필요한 목재가 충분히 마르면 나무를 기타의 앞, 뒤, 측면 그리고 넥 부분에 맞게 재단하고 일정한 두께로 깎아 낸다. 곡선 모양을 이루는 측면은 열을 이용해 가공하는데 이 공정은 기계의 힘을 빌리고 있다.
“초기에는 수작업을 했었는데 나중에 기계를 이용해 만든 측면 부분이 조금 더 정교하고 일정한 모양이 나와 지금은 기계를 이용하고 있습니다. 좋은 소리를 내는 기타를 만드는 데 기계의 도움이 필요하면 당연히 기계를 쓰는 게 맞겠죠.”
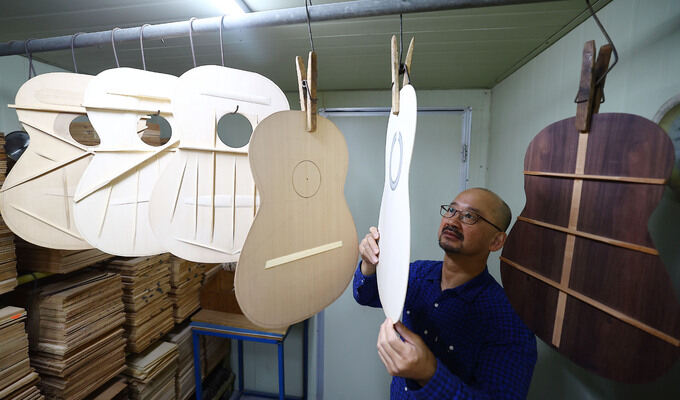
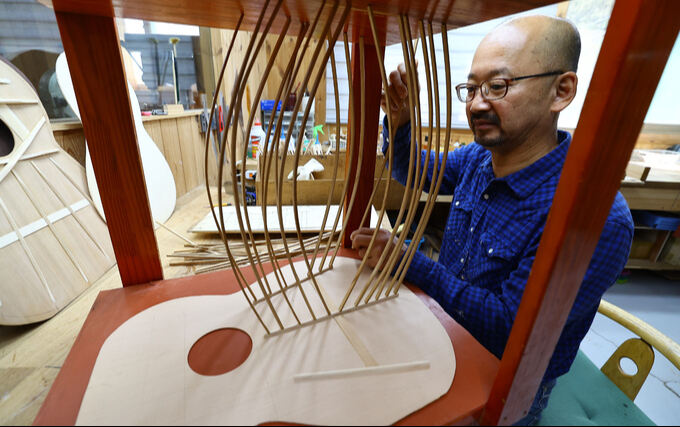
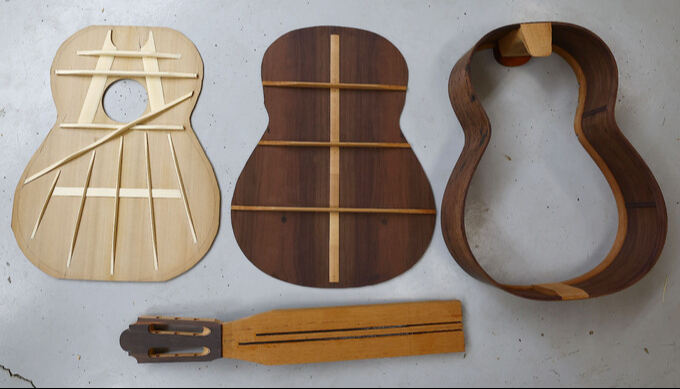
기타 앞판에 살을 붙이는 공정은 소리를 결정하는 과정이다. 장인이 스케치북을 여러 권 가져와 보여준다. 스케치북에는 장인이 설계한 다양한 음색의 도면이 그려져 있다. 이 도면에 따라 앞판에 살을 붙이면 각자 특색 있는 소리와 음량을 내는 기타가 만들어지는 것이다.
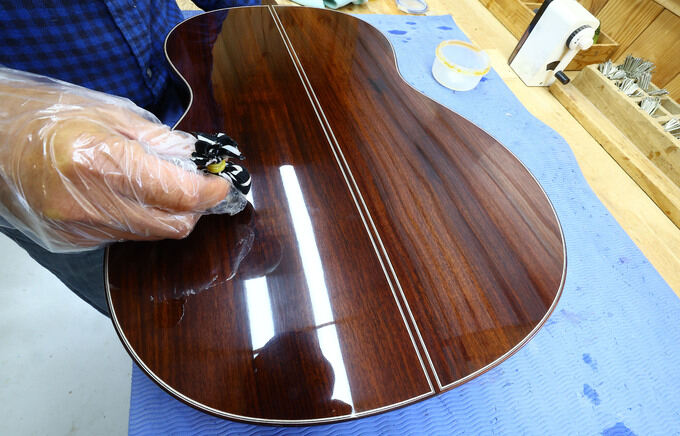
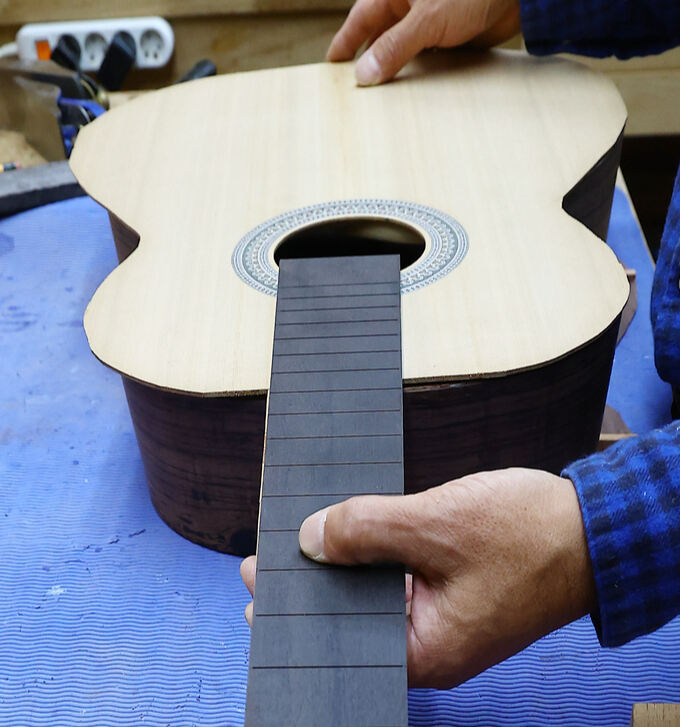
하나로 합쳐져 조립된 기타는 줄을 매기 전 칠을 해 광택을 내는데 도료는 벌레에서 추출한 천연 재료인 셸락을 사용한다. 50번 정도 칠하고 말리기를 반복해야 은은한 색감과 광택이 오랫동안 지속하는 본체가 만들어진다. 기자에게 보여준 공정은 기타가 만들어지는 수많은 과정 중 극히 일부분이라고 했다.
“제가 만드는 기타는 전문 연주가들을 위한 주문 제작이 많아 제작 기간이 짧게는 한 달에서 길게는 6개월 이상 걸리는 작품도 있습니다.”
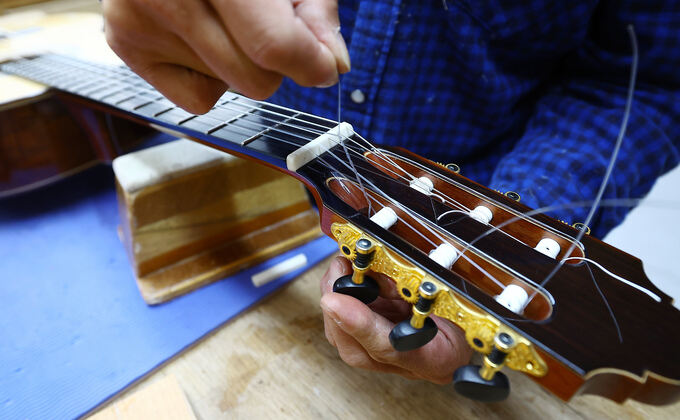
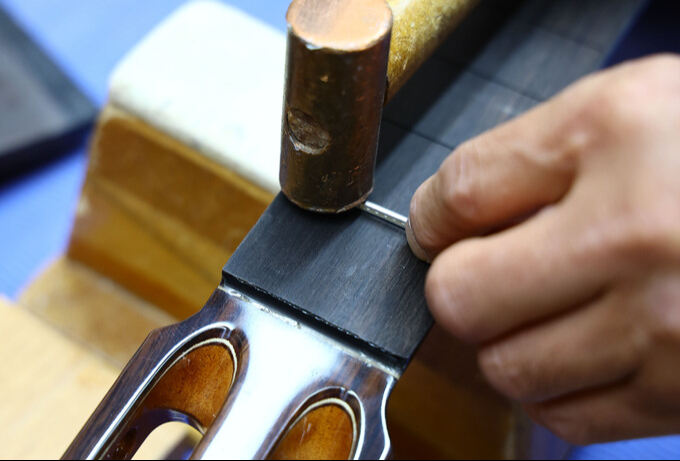
장인이 빠른 손놀림으로 기타에 줄을 매며 동시에 음계를 맞춰 조율한다. 조율까지 마친 기타를 들고 의자에 앉은 장인이 연주를 시작했다. 최종 점검의 과정이다.
“기타 하나를 만들려면 수백 가지의 공정과 약 만 번의 손길이 닿아야 합니다. 이번 작품은 조금 오래 걸렸지만 마음에 드는 기타가 나왔네요.”라며 환한 표정을 지어 보였다.
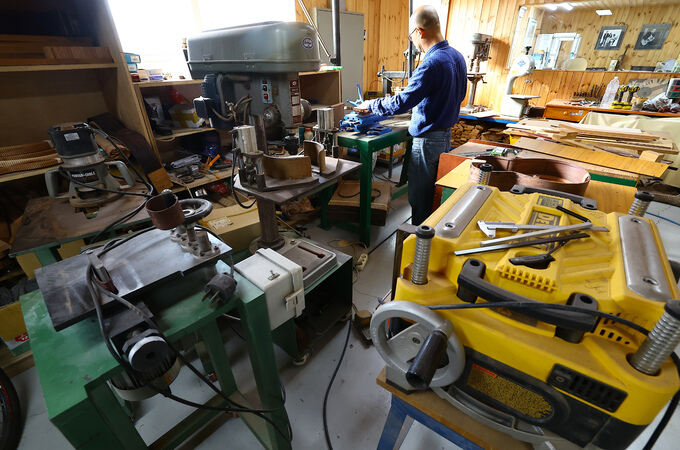
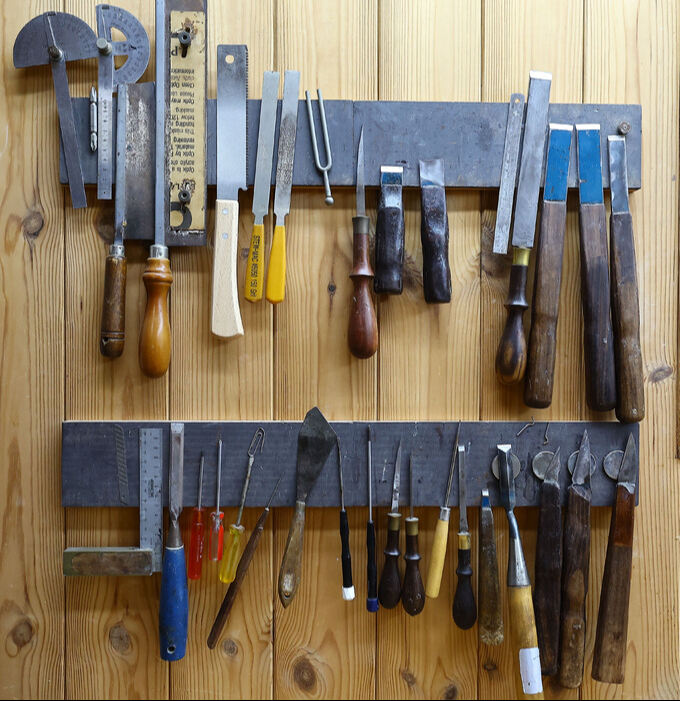
이주용 장인은 음대에서 클래식 기타를 전공한 연주가이기도 하다.
“연주가의 입장에서 기타를 만든다는 것이 제게는 큰 장점이죠. 항상 연주가가 표현하고 싶은 모든 음색과 음량을 그대로 내줄 수 있는 기타를 만드는 게 저의 영원한 목표입니다.” 수제기타를 만드는 장인의 작은 소망이다.
[ⓒ 세계일보 & Segye.com, 무단전재 및 재배포 금지]